3 Forms of Routine Water Well Maintenance

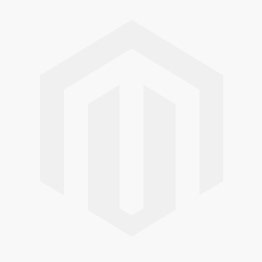
Well maintenance prevents major damage and keeps water clean and healthy. Learn about the common forms of routine water system maintenance with this guide.
Many people across the country rely on well water to drink, bathe, do the dishes, and much more. As such, these homeowners need to know that their wells are both clean and operational. Preventative maintenance helps avoid dangerous problems such as contaminated water, corroded pipes, or disrupted water flow. Routine maintenance allows homeowners to catch any problems that arise with their water system early, saving them from paying a lot of money in major repairs down the road. Learn about these common forms of routine water well maintenance and how they help homeowners preserve their water systems with this overview.
Flow Tests
A well’s rate of flow tends to decrease over time. There are many reasons why this might happen, including built-up mineral deposits, growth from microorganisms, or damage to the pump itself. Flow tests analyze the well’s ability to pump water and help determine what issues might be slowing it down. If debris and organisms within the well are limiting water flow, professionals can use chemical treatments to cleanse the system. If the problem stems from corrosion or other forms of pump damage, professionals can repair or replace pipes, valves, and other well materials.
Water Quality Tests
Water quality tests ensure that the water coming from a well is safe to use. Since homeowners use well water to drink and clean, these tests are among the most essential forms of routine water well maintenance. Annual tests for coliform or E. coli bacteria will make sure well water remains safe to use. Professionals can perform a well disinfection to eliminate these and other harmful microorganisms. Other tests—such as measurements for pH balance or total dissolved solids—should occur every couple of years. Additionally, homeowners should test water quality if they notice any difference in the appearance, smell, or taste of their water.
Inspecting Mechanical and Electrical Systems
Part of keeping a water system running smoothly is making sure the water pump, motors, electrical panels, and other mechanical parts are in good shape. A visual inspection helps professionals catch signs of erosion or other exterior damage. You can also check the electrical box for overheated motors or panels. However, a more in-depth inspection that checks valves, bearings, impellers, and other essential parts allows professionals to catch interior issues within the system. Evaluating these systems and repairing them as needed keeps the well in good shape inside and out.
As with any pipe or plumbing system, professionals working with wells must have the right tools at their disposal. Equip yourself with versatile inflatable well packers and other essential pipeline accessories to get the job done quickly, confidently, and successfully.
The information may be used but with no warranty or liability. This information is believed to be correct but should always be double checked with alternative sources. Strictly adhere to and follow all applicable national and local regulations and practices.