Weld Neck vs. Slip-On Flanges: Key Differences and Applications

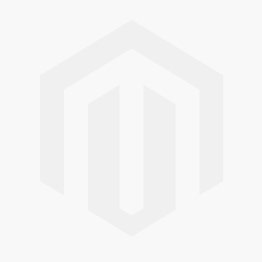
Flanges are indispensable parts of piping systems, providing leak-free connections that enable safe movement of liquids and gases. Comparing weld neck vs slip on flanges shows their different features which best match specific applications.
Weld neck flanges are strong and long-term connections designed for high pressure systems with their secure butt-welded attachment, while slip-on flanges offer simpler installation and more cost-effective pricing, making them suitable for lower pressure applications that don't need as much strength.
In this article we'll compare weld neck flanges and slip on flanges and their respective advantages and disadvantages, in order to help you decide which is most suitable for your piping system.
What Are Weld Neck Flanges?
Weld neck flanges are constructed to provide strong, secure connections in piping systems involving high pressure or temperature environments or fluctuating conditions. Their distinctive construction consists of a tapered hub connected by an extended neck that gradually transitions into the pipe - this ensures a seamless connection that minimizes turbulence or erosion at its junction.
Weld neck flanges stand out from their peers by featuring an eye-catching tapered hub, designed specifically to be joined to pipe through full-penetration butt welding for a strong and seamless joint. Additionally, their long neck enhances stability while equally dispersing stress over connections; essential considerations when designing high-stress pipe systems.
To further ensure the quality of these welds, tools like the Flange Weld Test Plug can be invaluable. This hydro test plug allows operators to monitor upstream conditions, isolate and purge the weld area, and perform the weld and hydro test of the weld joint using just one tool.
What Are Slip-On Flanges?
Slip-on flanges are a cost-effective and simpler alternative to weld neck flanges for low pressure piping systems. As their name implies, slip-on flanges slide directly over pipes and are held in place by two fillet welds, one inside and one out - making installation and positioning much easier than with weld neck designs.
Slip-on flanges are designed to be easily fitted over pipes and welded in place. Without the bulky hub and neck found on weld neck flanges, installation becomes less cumbersome and simpler. Two fillet welds hold them in place; however, unlike their full penetration counterparts these provide less structural strength and pressure resistance.
Compare Weld Neck Vs Slip-On Flanges: Examining Key Differences
Weld neck and slip-on flanges are two popular forms of pipe flanges designed to securely connect pipes while meeting specific pressure and temperature requirements. Their primary differences lie in design, installation techniques, and applications; here, we'll outline these key distinctions between weld neck and slip-on flanges to help you select the one that is ideal for your piping system.
1. Strength and Pressure Tolerance
Its Weld neck flanges offer greater strength due to their solid hub with full-penetration welding process and full penetration weld, which withstand higher pressures and temperatures than their slip-on counterparts with simpler fillet welds; they're best used in low to medium pressure applications.
2. Welding Requirements
Flange joints typically require full butt welds to strengthen and absorb stress, while slip-on flanges use two fillet welds instead, which provide less structural integrity but require two less complex welds for attachment.
3. Cost Considerations
Initial installation costs for weld neck flanges tend to be higher due to material and welding requirements; however, they could ultimately prove more cost-effective for higher stress applications over time. Slip-on flanges tend to be less expensive for installation; however, they may require additional maintenance expenses in the future.
4. Installation Complexity
Weld neck flanges require more skill and time for installation, while slip-on flanges can be installed more quickly, making them suitable for low pressure systems where strength isn't as paramount.
Short answer: weld neck flanges are ideal for high-stress environments where strength is of utmost importance, while slip-on flanges offer cost-effective and simpler installation alternatives for lower pressure applications.
Applications: When To Use Weld Neck Flanges Vs Slip-On Flanges
Ideal Uses for Weld Neck Flanges
Weld neck flanges are an excellent solution for high-pressure systems and locations where durability is of utmost importance, such as petrochemical plants, high temperature pipes and other critical infrastructures that rely on consistent operation under stress. Their design makes them suitable for use with hazardous fluids such as gasoline or even high-pressure fluids without becoming damaged over time - an invaluable quality that sets Weld neck flanges apart.
Ideal Environments for Slip-On Flanges
Slip-on flanges are well suited for low and medium pressure applications, such as water distribution, HVAC installation and some chemical processing conditions. Their ease of installation and lower initial cost make them an attractive solution where high durability is not a concern.
Choosing the Right Flange for Your Needs – Weld Neck Vs Slip On Flanges
When selecting weld neck or slip-on flanges for your application, consider these guidelines when making your decision:
- Pressure Requirements: For systems requiring high pressure and temperature conditions, weld neck flanges offer greater strength for high-pressure/high temperature applications; slip-on flanges work best in low to medium pressure systems.
- Installation Requirements: If your team of welders are experienced enough, weld neck flanges may be ideal. Slip-on flanges, however, are simple and straightforward for installation and use.
- Budget Considerations: Though weld neck flanges may initially cost more, they can reduce maintenance expenses in demanding situations. Slip-on flanges tend to be more affordable upfront but can result in higher inspection and maintenance expenses over time.
- Material Compatibility: Confirm that the material of your flange matches that of the fluids or gases within your system. Both types are offered in multiple materials to suit various chemical and physical specifications.
Conclusion
In summary, the main differences between weld neck and slip-on flanges lie in their design, strength and uses. In particular, weld neck flanges possess exceptional strength for use under high-pressure and temperature environments while slip-ons can only handle lower pressure situations.
Slip-on flanges, on the other hand, are easier to install and less costly; therefore, making them suitable for low to medium pressure systems with limited strength requirements and tolerance limits. Understanding these differences allows you to select an optimal flange type for your plumbing requirements.
Disclaimer: The information may be used but with no warranty or liability. This information is believed to be correct but should always be double checked with alternative sources. Strictly adhere to and follow all applicable national and local regulations and practices.
Regardless of these comments, it is always necessary to read and understand manufactures instructions and local regulations prior to using any item.