Cooling Loop Valve Replacement

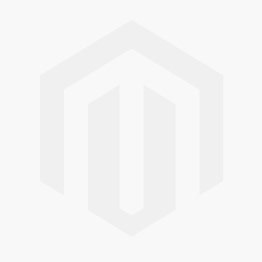
Innovator Industrial Services is the fastest growing specialty services provider in Canada, offering the “specialty maintenance and construction services required in maintaining high temperature and high pressure piping systems.” As the name implies, the firm emphasizes innovative, cost-effective solutions for the unique challenges posed by the complexities of pipe arrays in oil refineries, manufacturing facilities, and other large plants and factories.
Innovation is desperately needed in this industry, where ‘tricky’ is typical, and Innovator crews are trained in hot taps, field machining and cold cutting, laser inspection, airborne ultrasonic inspection, and the dozens of additional specialties called for in a typical week’s work. One recent valve replacement called for inventive thinking by Innovator and by Petersen Products, the vendor they called on to create a custom inflatable bag stop in a very tight space at an oil refinery.
“This was a cooling system loop with a valve closed and handle broken in a vertical run,” explains Innovator Operations and Quality Coordinator Darren Nisbet. “The system was working, so it wasn’t exactly an emergency. But clearly the valve needed replacing and there was no obvious way to isolate the valve and repair it without shutting the whole system down.”
One non-obvious way to isolate and replace the valve was to insert an inflatable bag stop into a T-shaped pipe joint a few feet below the broken valve—when inserted into the T and inflated, the right-shaped bag would seal off the joint and permit work on the valve. This type of insertion can be done with a hot tap, and that method was considered. But it wasn’t really necessary; a valve was available on the horizontal run leading into the T-joint, and could be used for bag insertion with no hot tap needed.
However, space was a problem. “We didn’t have a lot of room,” says Nesbit. “The typical launch assembly is five feet or so, and we had less than three feet to work with.”
To replace the valve without shutting down the cooling system entirely, Innovator needed a precisely formed, high-quality inflatable bag stop that would exactly fit the T-joint, and they needed a very compact insertion mechanism that could be used in the limited space available. That’s where Petersen Products came in.
100+ Years of Inflatable Innovation
Petersen Products has been making inflatable bags for sealing off sewer lines, piping systems, and other industrial uses since before 1916, when they custom-built inflatables for use in the City of Milwaukee’s sewer system. But they had never built an insertion system quite as compact as the one called for by Innovator’s project. The first idea was to attach the launch cylinder to the insertion point at a 30º angle so that the conventional five-foot launch cylinder could be set diagonally in the narrow space available. But after consideration, Project Engineer Kurt Kissinger felt this solution wouldn’t work well. “Basically, due to the forces in the launch cylinder, we felt that the inflatable and the insertion rods wouldn’t reliably negotiate the 30º bend called for,” he explains.
Plan B was to remove the short section of horizontal pipe between two valves to allow a straight insertion into the valve/entry point, and to create a cylinder that could be bolted directly to the valve. This cylinder was just 32 inches long and used one-foot ram sections to push the inflatable into place. “We’d never done it quite this way before, though we’d done something similar with a sliding tray designed to launch through butterfly valves,” says Kissinger. “But we were sure it would work, and pitched the idea to Innovator with a sketch.”
Successful Innovation
After review, Nisbet agreed that the modified launch cylinder would work in this oil refinery’s particular situation. And he even liked its innovative nature. “Part of my job description is to look for new, cutting edge solutions for this type of work, and I appreciated that Petersen had come up with something new and practical here. Cost-effectiveness was also a factor—this compressed launch cylinder allowed us to use the existing valve as an insertion point, and avoid the work of welding on a new fitting.”
But Nisbet’s review and approval wasn’t the only scrutiny required; because the Petersen launch cylinder was brand new in some ways, and because maintenance engineers at oil refineries tend to be, understandably, quite conservative, he also needed approval from refinery staff. Fortunately, “we explained it to our clients and they had their engineers look at it, and ultimately they agreed that it was a good solution and should work.” One factor in obtaining refinery approval was the (literal) low pressure and temperature of the cooling system water—though not entirely risk free, low pressure systems are generally much safer to maintain and repair. Though Petersen inflatables have been used in extreme environments, such as deep sea oil platforms and in high-pressure, high-temperature industrial systems (some involving caustic or corrosive liquids or gases), the refinery cooling system water was at 110ºF and pressures were relatively low.
With the new, innovative launch cylinder approved, things moved quickly. Petersen Products fabricated and shipped the custom cylinder in less than a week, and Innovators received it on a Monday morning, assembled it for a ‘dry run’ at their yard Monday afternoon, and used it Tuesday, in the brief window provided by refinery staff.
No Surprises
“We were given an eight-hour window to do this work, and ended up completing everything in just seven hours,” says Nisbet. “There were no surprises.”
The Petersen inflatable was in place for about three hours of the eight-hour project window. Work began with removal of the horizontal pipe section between two valves, placement of the reduced length launch cylinder, and insertion of the compressed, 10-inch inflatable through the 8-inch valve opening and into the T-joint. Once set in place with the one foot long rod sections, the inflatable was inflated to 120 psi with air pumped into the cylinder’s inflation port and through the hollow rod sections. An injection valve was placed to verify the seal. “The broken valve was definitely isolated, with just a little trickle for ten seconds or so,” says Nisbet. “That was just the standing water in the vertical section, and expected.”
With the valve isolated, it was a simple matter to remove and replace it. And after this work was done, it was also a simple matter to deflate and withdraw the custom Petersen inflatable, detach the innovative launch cylinder, replace the horizontal pipe section, and restore the cooling loop to full functionality.
In the end, this tricky repair in a cramped space was completed with no system shutdown, cost-effectively, with a solution that required substantial innovation in a tight schedule from two different companies. But for all that, Nisbet says, “In a way, this was actually a straightforward project, it just called for a unique design to work in the tight space we were dealing with. Petersen’s design expertise and flexibility were really appreciated, and helped keep this project simple and safe, despite the challenges.”