How to Mitigate Risks of Hot Tapping

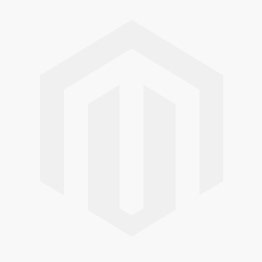
Hot tapping is a process that allows pipeline repairs or expansion to be completed without disrupting normal operations or depressurizing the system. The benefit of hot tapping is that sections of pipeline can be isolated and flow can be stopped with minimal downtime and without stopping production.
Due to the nature of this repair there are inherent variables to consider to mitigate risks. It starts with a thorough knowledge of these types of repairs and experience followed by a good plan. When it comes to utility lines, hot taps mean that service does not have to be interrupted during maintenance. Hot tapping is also referred to as line tapping, pressure tapping, pressure cutting, and side cutting.
Hot Tapping Risks And Dangers
Hot Tapping procedure should only be considered when it is impractical or impossible to complete repairs or add a new pipeline branch any other way. The reason being is that there are some serious hazards and dangers that can occur when using this process.
Hot tapping a pipeline consists of two primary phases:
- The process in which the hot tapping machine is attached to the piping system.
- This may be done by bolting, clamping, brazing, or welding a hot tap saddle
- Mechanically cutting a hole into the pipeline wall
- This may be done with a specialized hot tapping hole saw
The principal dangers lie in the fact that when hot tapping you don’t depressurize the pipeline and so are dealing with high pressure and/or high temperature situations. Plus, in certain circumstances you have to weld the hot tap machine to the pipeline, there is also a danger of igniting combustible gases or material.
The biggest issue with welding on the saddle is that you use the pipe or vessel as a backer for the weld. Burn through can occur when welding onto a pressurized pipe if the area beneath the weld pool is not strong enough to contain the internal pressure of the pipeline. Typically, the outside of the pipe can be cleaned and ultrasonically tested (UT) to insure that the metal area under the weld is known. Unstable decomposition of the flow material can also be a danger and result in violent reactions when heated under pressure.
Another danger is hydrogen cracking in carbon steel pipes, which is more likely to happen when hot tapping in comparison to other welding situations, due to the flowing product increasing the rate of heat flow from the weld region. This leads to shorter cooling times, with an associated increased risk of forming hard microstructures and thus greater susceptibility to hydrogen cracking. However, this issue can be controlled via appropriate welding procedures and understanding of the metallurgical process.
Hot tapping can be done on non-metallic pipes such as HDPE, however, these pipelines have other issue of concern such as lower strength and sealing with gaskets and mechanical joints. Also, the pipes cannot carry as high of a load as metallic pipes and vessels.
Copper pipes can also be hot-tapped. These are typically smaller in diameter and can have the hot tap saddle brazed, welded, or bolted onto the pipe or vessel.
How To Mitigate Hot Tapping Hazards?
Due to the dangerous nature of hot tapping, it’s important to take the proper steps to lower the risk of accidents and injuries. First, it’s crucial that everyone involved be trained and familiar with the process, welding procedures (if required), and the use and location of all necessary tools and equipment. Next, a preliminary risk assessment should be done to check whether hot tapping can be done safely at the specified location of the pipeline. OSHA has standards such as 1910.252 for welding, cutting, and brazing. Hazard communication is very important and lock-out tagout procedures should be followed. Petersen Products follows a variety of codes and standards such as API, ASME, ISO, and NBIC.
The following parameters should be considered before using a hot tap:
- Size and thickness of pipe or vessel wall
- Minimizing hot tap size (use Petersen Products inflatable line stop or flow stop plugs)
- Vessel wall integrity, corrosion issues, and material
- Operating pressure and temperature
- Media flowing through pipe or in vessel
- Fluid characteristics
- Velocity / flow in pipe or vessel
- Metallurgy / chemistry compatibility of all materials in contact with fluid (such as seals)
- Welding considerations, Metal Temp, Heat input of weld / Electrode/filler size, etc..
- Hazards and contaminants at location / worksite
- Fire watch, permits, barriers, contingency plan, end user safety policies, as required
- Local codes and standards
- Special considerations; above or below grade, confined space, decks of floating roof tanks, or upstream valves, tanks in service or other.
Safety Requirements Before Hot Tapping
In metallic pipes metal thickness should be measured by ultrasound (UT) devices, typically shear wave is preferred rather than straight beam. Any other method of measurement needs to be approved by owner inspector. The thickness should be exactly measured at the location where the welding is expected to be done. It is recommended to measure thickness over a 2” band and the recommended minimum thickness for hot tapping is about (3/16”) 5.0 mm. The material should also be cleaned, preheated, and/or PWHT according to acceptable welding procedures. Hot tapping procedure should avoid the weld seam in pipeline or vessels if possible. Use extreme caution on wall thicknesses less than ¼” thk. In thin wall carbon steel hot taps, it is generally recommended to monitor heat input and use electrodes 3/32” or smaller on the root pass to prevent cracking, however it may increase risk of cracking in high carbon equivalent metals. It is recommended to use 1/8” dia or larger on subsequent weld passes.
The metallurgy of the hot tap fitting and the filler material must be compatible with the metallurgy of the equipment to be welded or hot tapped. For example, low hydrogen electrodes are often advisable to minimize weld cracking problems in carbon steel or a high purity flux and filler on brazes on copper pipe. Special welding consideration may be needed for high tensile strength steels to avoid weld cracking and the need for post weld heat treatment. Support of the pipe or vessel when PWHT should also be considered. Always follow an acceptable welding procedure for the job. Petersen Products can help guide you in your weld-on saddle applications no matter the alloy.
Testing Hot Tap Saddle Integrity After Welding
After welding, the hot tap nozzle should be tested at the pressure calculated by the design engineer. If pressure testing is done above this calculated value, the parent pipe can buckle inwardly. The larger the branch of the hot tap, the higher the risk of buckling. The testing medium should be selected based on the temperature of the fluid flowing through the pipeline system to ensure an accurate test.
The isolation valve to be installed on the hot tap flange should be hydro-tested in the shop prior to installation to ensure seat sealing. The gland packing should be changed prior to test to make sure that there are no leaks during the pressure test and subsequent hot tapping operations.
Take The Necessary Precautions
Before beginning a hot tapping job, the maintenance, inspection, and operations crew on-site should meet with the contractor and prepare a risk assessment for conducting the hot tap safely. This assessment should include a contingency plan in case of a mishap during the process and there should be clear lines of communication between the hot tap crew, supervisors, and control room in case of an emergency. The fire department should also be informed in case they need to respond to an emergency fast.
Lastly, the crew should be informed of the hazards of the fluid flowing through the pipe, ensure enough ventilation and lighting in the work area, and only keep the minimum number of required personnel near the hot tap location while welding.
Contact the Petersen Products team with any questions concerning hot tapping procedure precautions.
The information may be used but with no warranty or liability. This information is believed to be correct but should always be double checked with alternative sources. Strictly adhere to and follow all applicable national and local regulations and practices.