How to Use a Bypass Plug for Pipeline Testing or Isolation

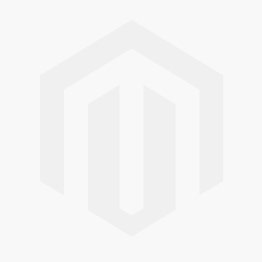
Bypass plugs are commonly used for monitoring, testing, and repairing pipelines in waterworks, sewer and plumbing systems, oil and gas infrastructure, chemical industries, and more. They are designed to isolate a section of the pipeline temporarily while still allowing the fluid or gas to flow through. The primary advantage to using a bypass plug for pipeline testing, maintenance, or repair is that you don’t have to shut down the system or completely stop the flow during the project.
When to use a bypass plug
Pipeline testing and repair jobs often require cutting off flow to part of the system, which involves blocking each side of the section, draining it, and ensuring that no contents move through it while the work is being completed. The problem is that just blocking the flow means that the entire system may have to be shut off, causing severe disruptions to often critical services. To avoid this situation, bypass plugs are used to divert the contents around the isolated section, ensuring service continues.
How bypass plugs work
When choosing a bypass plug, there are two types available: mechanical and inflatable. The advantages of mechanical options are that they are often easy to install without tools and they can provide a long lasting or permanent seal. The drawbacks are that they are for a single size pipe ID, and while they may be designed for any size pipeline, handling and installing large mechanical plugs can be difficult. When installed through a smaller manway they must be assembled in the pipeline from smaller sections.
An inflatable bypass plug is placed in the pipeline and then inflated to press against pipe walls to create a seal and help block from slipping. Their primary advantages are that they can often fit multiple pipe sizes, including very large diameter lines, are able to be installed through smaller openings when deflated, and are flexible for installing in and through irregular shapes. They may also be used as a grout bag for permanently abandoning a pipeline.
Whether mechanical or inflatable, all types of bypass plugs work by having a tube in the center of them that allows the pipe’s contents to flow through. That tube is then attached to a hose that either connects to another bypass plug down pipe, or that connects to a pump that moves the contents up and over the isolated section. In both situations, the flow is maintained, but it’s diverted around the part of the pipeline being worked on.
Another option is an inflatable Annular Seal (like a donut or torus) where the outer seal contacts the pipe to be blocked and the inner seal holds the bypass pipe. These are typically custom configurations where you would need to provide the inner seal diameter, outer seal diameter, head pressure to hold back and any unusual chemical or temperature requirements.
Choosing the right bypass plug
There are several factors that you need to consider when choosing the best plug for your specific project:
Pipe dimensions:
- What is the internal diameter of the pipe requiring plugging?
Bypass requirements:
- What volume must the bypass handle? (Consult your project engineer for this information)
Pressure specifications:
- What is the maximum pressure the plug must withstand?
- Is the pressure source air/gas (measured in PSI) or liquid like water/sewage (measured in feet of head)?
Installation access:
- What is the size of the opening (e.g., manhole diameter) through which the plug must be inserted?
- Note: Some plugs, like Multi-Flex® and Muni Balls, are flexible allowing bending or installation in an Elbow or Tee.
Temperature considerations:
- What is the temperature of the material being blocked?
- Caution: Natural rubber plugs should not be used above 125° F (52° C) due to melting risk.
- Mechanical and inflatable plugs with synthetic material like Kevlar and Viton plugs may be used for up to 400° F.
Chemical compatibility:
- Will the plug encounter oils, hydrocarbons, or petrochemicals?
- Note: These substances may degrade natural rubber. Plugs can be made with different types of material for size, pressure, temperature, and chemical requirements. Consult the manufacturer for applications involving such materials.
It’s crucial that the bypass plug you use meets all pressure, temperature, and chemical conditions, or else it could fail during operation.
Tips for installing bypass plugs
When completing a pipeline testing or repair job, it’s important to take the proper steps during plug installation.
- Check your plug for punctures, bulges, cracks, and corrosion.
- Use an accurate pressure gauge when inflating pneumatic bypass plugs and monitor air pressure regularly while the plug is in use.
- Remove debris from the pipeline before the plug is installed—gravel, broken glass, and exposed rebar can puncture your inflatable plug.
- Make sure you inflate the plug to the exact pressure recommended by the manufacturer.
- Once the job is finished, first relieve any back pressure before deflating the inflatable bypass plug, and do not remove it until it has been completely deflated.
Always refer to the pipe plug instructions manual for proper use and maintenance.
If you have any questions about using a bypass plug for pipeline testing or maintenance, please contact our team today.
The information may be used but with no warranty or liability. This information is believed to be correct but should always be double checked with alternative sources. Strictly adhere to and follow all applicable national and local regulations and practices.