Inflatable Bag Stops enable critical plant maintenance without shutdowns

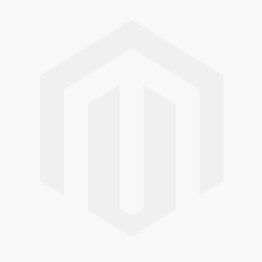
Furmanite, the international plant and pipeline maintenance firm, is big enough, experienced enough, and innovative enough to have developed multiple specialties focused on the demanding task of repairing and rehabilitating critical plant and refinery processes while minimizing downtime, or avoiding it altogether. One such specialty is bag stopping, where custom-made bags or plugs are inserted into pipelines while deflated, and inflated with air, water, or various gases at sufficient pressure to seal off the line and isolate downstream sections, sometimes for weeks at a time. “We do about 50 bag stops annually,” says Technical Support Manager Ralph Hawkins. “Some of that is in hospitals or in commercial projects like shopping malls. But most of our work is in the petrochemical industry—I work with two technicians and we fly all over the country.”
The advantage of a bag stop is that fluids or vapors can be stopped conveniently close to repair sites, usually far downstream from available shutoff valves, so that fewer plant processes are affected and rerouting of affected lines is minimal. The inflatable bags Hawkins installs are made to suit for him by industry leader Petersen Products, and are quick to install, cost-effective, and often relatively simple compared to other available methods. And they’re not just used in plant environments; very large bags, several feet in diameter, are used in storm and sanitary sewer projects, and highly customized inflatable plugs have been used in extreme situations; in 2010, for example, a Petersen inflatable tunnel seal was inserted and inflated 420 meters below ground level by a remotely operated vehicle as part of a project that successfully deflooded deep levels of a Saskatchewan uranium mine.
“Bag stops are certainly beneficial, cost-wise, compared to mechanical stops,” says Furmanite Account Manager Andrew Simcik. “They’re not for every situation—for example, we’re less likely to use them when we’re dealing with corrosive materials—but when they meet our criteria, they’re very effective and we’ve never had one fail.”
Bag stops accomplished with inflatable plugs are, in other words, a line stopping solution that is applicable in many plant and refinery repair situations. The following two case studies of bag stop use are a study in contrasts, demonstrating the versatility of this useful plant repair technique.
Green Lake, Texas
In October 2014, workers at a refinery in Texas noticed a distinct odor coming up through a cement slab in the plant interior—that’s never a good sign. To investigate, the slab was removed and subsoil was excavated, revealing a cracked weld in a six-inch line, ten feet below grade. “They realized they had a big problem with no obvious solution, so they covered it back up and started working with Furmanite,” Hawkins explains. “We’ve been working with them since then, to come up with the right repair techniques, and waiting on the optimum time to get in and do the work.”
A bag stop turned out to be a key component of the overall solution. A mechanical stop in an appropriate upstream location would have required slab removal and at least ten feet of excavation in active areas, something plant managers wanted to avoid. “In addition to disrupting work, a mechanical stop would have been expensive, and technically difficult,” Simcik explains. “This was an ideal situation for a bag stop.”
Fortunately, a four-inch riser was available nearby; Hawkins could slip a deflated bag through the four-inch riser, and inflate it inside the six-inch line. “The bag and pipe sizes were typical,” Hawkins says. “But the length of the riser was a little unusual—eight feet. We made a nozzled ram—a length of pipe—that allowed us to push the plug all the way through the riser and into the six-inch line, then inflated to 22 psi using utility air pumped through the ram. It all went well.”
The six-inch line was low pressure, and it carried various waste materials including hazardous vapors and liquids. Hawkins ordered the bag directly from Petersen, a process that he says is collaborative; “I had a good idea of what we needed in this case, the dimensions were standard. But they really are experts. I usually describe the dimensions needed, and the conditions the bag will be operating in, like the hazardous vapors here, and if a standard bag isn’t appropriate they will design and build a custom bag for us, usually in just a few days.”
Hawkins often keeps air lines hooked up to the bag stop for the entire project; “They don’t fail on us, but they can develop small leaks at the connections or sometimes they get small rips or holes during installation. If this happens, a constant air supply will usually keep the bag at more than adequate pressure to hold the seal.” As an additional safeguard, Petersen supplied an electronic sensor that measures pressure at the bag and sounds an alarm if pressure drops below a specified psi.
On this project, the bag was in place for about a week. Pumps and temporary lines were used to bypass the plug and work area, diverting waste to a holding tank. At project completion, the plug was deflated with a commercial vacuum, and withdrawn through the four-inch riser. The plug held with no issues for the entire project, and plant production was not affected.
Corpus Christi, Texas
Another Texas refinery project, which took place in nearby Corpus Christi, presented different challenges. It was a larger line, 16-inches, supplying unfiltered river water at 80 psi for filtering and use in most operations. “This line supplied all the water for three pumps that kept the whole plant running,” Hawkins explains.
One of the pumps needed maintenance; a routine task, but a failing valve made it difficult to isolate the pump, so all three pumps would be affected. This meant that all repairs had to be accomplished in a short window, just four hours, so that pumps could be supplied from a backup tank with an emergency water supply.
This project highlights another excellent feature of Petersen inflatable pipe plugs—in most cases, they can be installed very quickly, and withdrawn at project conclusion in a matter of minutes. Petersen supplied a 16-inch bag made of Ballistic Nylon calendared with nitrile. Installation posed no special challenges; “We were able to insert and inflate the bag, then let it settle to check for stability, all within a half hour or so,” Hawkins says. This bag was inflated to 120 psi, again with utility air that was kept hooked up for the entire project. Maintenance work was successfully completed, the bag was withdrawn, and water supply resumed within the four-hour window.
Production never stopped. Plant managers sent an email to Simcik, saying, “Thank you for a successful valve replacement job. The valves were changed in good time, there were no incidents despite the inclement weather, and the plant was totally unaware of the change out. Well done!” (emphasis added)
Quality Control & Reuse
Petersen inflates all their inflatable bags to at least 1 ½ times projected use pressure prior to shipping, to verify that there are no leaks and that inflation valves and manifolds are holding. And Furmanite will often inflate and test prior to insertion as well. In some cases, best practices even call for insertion and inflation in a constructed ‘model’ of the specific project pipeline configuration, to be sure that unusual insertion conditions will not be a problem when it counts. “Petersen is very reliable,” Simcik says. “We’ve never had one of their bags fail, and they’ve been our exclusive supplier for at least 20 years.”
Furmanite crews are specially trained and certified for inflatable bag stops, and bag stop projects require that experienced personnel be onsite for this specialized procedure—Hawkins has been filling that role for five years, overseeing about 50 bag stop projects annually.
Inflatable plugs can be reused. “Yes, if there hasn’t been any damage, and they haven’t been exposed to caustic chemicals, we reuse bags,” Hawkins says. “We send them back to Petersen for refurbishing.
Simcik adds that refurbished bags are typically used as backups. “We like to have at least two bags available for any given project, in case a bag gets damaged during installation, or something goes wrong during the project. If we have to, we’ll go ahead and order two bags, but if we have a refurbished bag available we’ll ship it to the site and use it. We have complete confidence that most bags can be reused.”
Bag stopping is an efficient, fast, cost-effective alternative to mechanical stops, and are just what’s needed in many situations. So it’s good to be aware of them; but as Simcik says, “Somehow, they don’t always come to mind for our customers—they tend to think of mechanical stops as the only possibility, so often it’s up to us to suggest a better alternative.”