Petersen Inflatable Line Stop Keeps an Oil Sand Facility Producing

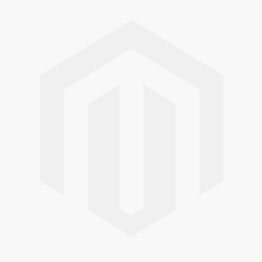
The Foster Creek Project began life as a Cenovus Energy oil sand pilot project, and the company is proud of it. Their website says:
“Foster Creek is located about 330 kilometres northeast of Edmonton, Alberta on the Cold Lake Air Weapons Range—an active Canadian military base. The oil at Foster Creek sits about 450 metres below the surface—so deep that we have to use technology called steam-assisted gravity drainage (SAGD), to drill and pump the oil to the surface. Foster Creek began as a pilot project in 1996 and started commercial production in 2001 as the industry’s first commercial project to use SAGD technology. Foster Creek is one of the most efficient SAGD facilities in the industry because of our low steam to oil (SOR) ratio. A low SOR means it uses less water and natural gas and creates fewer greenhouse gas emissions to produce a barrel of oil than other oil sands facilities of the same size. In 2015, we produced an average of 130,000 gross barrels of oil per day.”
Put another way, this is a spectacularly successful project in the challenging oil sand industry, and Foster Creek has steadily expanded in several phases as production has ramped up. But that very success created a challenge in 2012 when a project expansion called for the installation of a flare system. “Foster Creek had been using a pop tank to process dangerous gases for several years, and that was fine when it was a small plant, and the tank was remote,” explains Colin Norman, a Cenovus Staff Project Engineer at the time. “But with the increased production and more infrastructure on site, the pop tank was becoming unsafe and a full flare stack system needed to be installed.” And that was a major undertaking; about 250 plant subsystems fed into the pop tank, and all had to be diverted to the new flare stack. “Schematically, it was a lot like a river tributary,” says Norman. “A spaghetti network fed into seven or eight major lines, and then to the tank.”
The problem, of course, was production—margins are thin in oil sand projects and for economic reasons Cenovus wanted to avoid out a significant break in production. There was an opportunity to do the work during a scheduled turnaround, but a little calculation made that look untenable. “Just isolating the existing systems would take the entire shutdown time—with no work done on the flare system!” says Norman. “So that was a non-starter.”
The eventual plan called for a live switchover to the flare stack, using hot taps to progressively isolate and divert eight plant sections. This was a major undertaking with a lot at stake—the pop tank system, after all, was a major safety feature. Still, the risks were analyzed carefully and safe implementation of the plan was definitely feasible. But there was one major challenge to resolve first—just how would pop tank lines be safely closed as needed?
Developing and Testing a Safe Solution
For very good reasons, isolation valves are not typically installed in flare system or pop tank lines. “Historically, valves that have failed or been closed inadvertently have caused serious problems, so they’ve become taboo in these situations,” Norman explains. That’s why hot taps were needed here, and why some alternative to valves were needed. Typically mechanical line stops called stopples are used with hot taps, but stopples wouldn’t work on this project.
“Just before this project got underway, ABSA (Alberta Boilers Safety Association) had changed their guidelines to rule out conventional ‘size on size’ hot tapping, and without that, stopples weren’t practical,” explains General Manager Trevor Hull of (project contractor) Red Flame Industries. Looking for alternatives, Hull eventually came across Inflatable Line Stop™ inflatable pipe plugs, also known as ILS™ plugs, from Petersen Products, also known as bag stops. The basic idea is simple; correctly sized bags are collapsed and inserted into pipes through a hot tap, then inflated at sufficient pressures to seal off and plug lines. This looked like a good solution, but there were a lot of details to work out.
Red Flame now uses Petersen inflatable ILS plugs routinely, about “Once a quarter,” according to Hull, and inflatable bag stops are a proven technology with a long history of use, particularly in sewer and water lines. But Foster Creek was Red Flame’s first use of this solution, and given the high stakes of this particular project they had a lot of questions about proper application.
To resolve these questions, Red Flame’s owner flew to Fredonia Wisconsin to consult personally with Petersen President Phil Lundman, and bag tests were conducted over a six-month period on simulated Foster Creek lines. “It was mostly trial and error,” admits Hull. “But as we practiced with the bags and hot tapping, we came up with some very good ideas.”
One of those ideas, which appears to be a first in the oil and gas industry, was to use two inflatable plugs downstream of the pop tank when isolating plant sections. This important innovation resolved several project issues:
- Most obviously, two plugs provided redundancy in case of a bag failure—always a good idea when dealing with emergency systems.
- Less obviously, but crucially, using two plugs provided a way to test the line stop. After plugs were inserted and inflated, Red Flame could raise the pressure in the space between the plugs, and verify that both plugs were sealed. Without this interstitial space, there was no good way to raise pipe pressure and verify seal of a single plug. “Basically, the bags were working as valves in this project, and we had to be able to prove they would hold,” says Norman. “There was no way to do that with a single bag in a low pressure atmospheric piping system.”
- For even more assurance of seal, Red Flame could pump a liquid sealing agent into the interstitial space at relatively high pressures. In practice, this worked a bit like tire sealant, by instantly filling any gaps or cracks caused by scaling in lines or bag settling. And it was another way to test, verify, and monitor the line stop pressurization during use.
In Practice
Petersen Products manufactures inflatable bags to suit specific project needs, including pipe dimensions, operating pressures, and caustic materials in lines. At Foster Creek, operating pressures weren’t particularly high and most lines transported sour gas, so several fairly standard bags were supplied, made of Kevlar and Viton rubber (a fluoroelastomer polymer), with diameters of 10, 12, and 24 inches.
Hot tapping and insertion was straightforward. On 10-inch and 12-inch lines, two hot tap connections were made and bags were inserted through each. On 24-inch lines, just one hot tap was needed. “On bigger lines, we could put in a tap large enough to insert two deflated bags at once,” Hull explains. “On the smaller lines, that size hole would have weakened the pipe unacceptably.”
In all cases, a gap of about eight inches was left between bags. After insertion, bags were slowly inflated with nitrogen to 100 psi, seals were checked with nitrogen pumped between bags at 20 psi, and sealing agent was pumped in, also at 20 psi. “The Petersen plugs held pressure and seal very well,” Hull says. “We never had one fail during the project.”
Up to four inflatable line stops Inflatable Line Stop plugs might be installed at various phases of the switchover, and were left in place up to three weeks. Plugs were routinely reused during the switchover, moved from section to section as needed. “It’s nice that they’re reusable,” says Hull. “Because they are a little expensive.” While installed, all plugs were connected to pressure gauges and Red Flame staff monitored bag pressure hourly.
During construction, were the Iinflatable line Line Sstop plugss ever put to the ultimate test? “Oh yes,” says Hull. “On three different occasions, the plant went to full flare and everyone was evacuated. When this happened, line pressures could abruptly rise to about 50 psi, and I’m happy to say the Petersen plugs held every time.”
This was a successful project—the switch to the flare line was completed efficiently and safely, with no unscheduled breaks in Foster Creek production. Red Flame and Cenovus can be proud of a solution that kept workers safe during a dangerous project, and their innovative use of inflatable line stopsInflatable Line Stop plugs has already become a new standard in the oil and gas industry.
# # #
Angus W. Stocking, L.S. is a licensed land surveyor who has been writing about infrastructure since 2002.