What Are Mechanical Pipe Plugs? An A to Z Guide

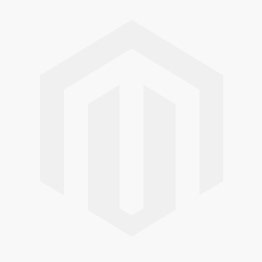
Mechanical pipe plugs are essential devices for pipeline maintenance. They temporarily seal or isolate sections of pipelines making the flow more accurate and controlled. Additionally, they are referred to as mechanical pipe stoppers, pipe bungs, pipe test plugs, and line stops as well.
In pipeline maintenance, mechanical pipe plugs are one such indispensable tool that secures temporary seals, facilitates pressure testing, enables emergency repairs, and offers versatility across different applications. These tools serve a crucial role with reliability, ease of use, and effectiveness, ensuring the integrity and smooth functionality of pipelines across various industries.
Are you searching for the best mechanical pipe plugs? You are in the right place!
In this comprehensive guide, we delve into the intricacies of mechanical pipe plugs, offering invaluable insights into their evolution, types, applications, and future trends.
The Evolution of Mechanical Pipe Plugs
The evolution of mechanical pipe plugs can be traced through three distinct generations. Technological advancements in mechanical pipe plugs are the main reason for the evolution.
Initially, mechanical pipe plugs were simple in design. Although these designs are not flexible and can create problems in the long run. However, as industries demanded more robust solutions, innovations emerged.
1. First Stage- One significant advancement was the development of two-piece plugs, featuring a ring and pin design. This design spreads the load more evenly, reducing the risk of damage to the tube or tube sheet during installation.
2. Second Stage- Further, the technological improvements led to the creation of mechanical pipe plugs capable of withstanding higher pressures. These plugs incorporated serrations on the exterior and utilized hydraulic mechanisms for installation, ensuring a secure seal even in demanding environments.
3. Third Stage- Moreover, advancements in materials science have played a crucial role in enhancing the durability and performance of mechanical pipe plugs. Modern plugs utilize high-strength materials engineered to withstand extreme conditions, such as corrosion, temperature fluctuations, and chemical exposure.
Additionally, innovations in manufacturing processes have enabled tighter tolerances and precision engineering, resulting in large-diameter mechanical pipe plugs and high-pressure pipe plugs. These plugs offer reliable sealing properties and ease of installation.
Overall, technological advancements have propelled pipe plugs from rudimentary designs to sophisticated solutions capable of meeting the diverse needs of modern pipeline maintenance, ensuring reliability in critical infrastructure operations.
Types of Mechanical Pipe Plugs
For long-term or permanent plumbing installations, mechanical plugs (with a range of.39 to 18 inches) are utilized.
1. Blocking Mechanical Pipe Plug- DWV systems are tested with these specific plugs. They are sealed for testing and fit into pipes with a maximum diameter of 6 inches.
2. Bypass Mechanical Pipe Plug- Residential or commercial pipe installations and repairs are done with these plugs. They enable testing and monitoring for pipes up to 18 inches and are used when system repairs are necessary but wastewater must still flow.
Uses of these pipe plugs-
The majority of mechanical plugs are made to block the gateway. The main purpose of mechanical pipe plugs is to test DWV (Drain-Waste-Vent) systems, although they can also be utilized in bigger waterworks applications as necessary. Other applicaitons include: force and water main, lift stations, nuclear cooling lines, fire protection lines, special plant situations, irrigation supply lines, and many other projects where isolation is required for testing and construction. Certain mechanical plug alternatives, including Clean Out Coverings and Pipe Hubs, are made for certain uses and have specialized qualities like chemical resistance and locking capability.
Advancements in Material Technology
Traditionally, pipe plugs were predominantly made from materials such as rubber, plastic, or metal. However, recent innovations have introduced wider materials engineered to withstand the rigorous demands of pipeline maintenance.
Some modern material technologies used in mechanical plugs are-
1. Synthetic Rubber Compounds:
Synthetic rubber compounds offer exceptional resilience and elasticity, ensuring tight seals in pipeline applications.
● These compounds exhibit high chemical resistance, allowing mechanical pipe plugs to withstand exposure to various corrosive substances commonly found in pipelines.
● Synthetic rubbers can tolerate a wide range of temperatures, from extreme cold to high heat, ensuring reliable performance in diverse operating conditions.
2. Advanced Plastics (e.g., Polyurethane, Nylon):
Advanced plastics such as polyurethane and nylon provide superior strength-to-weight ratios, making them ideal for high-pressure sealing applications.
● Plastics offer excellent corrosion resistance and dimensional stability, ensuring long-term durability in harsh environments.
● Plastics can be engineered to exhibit specific properties, such as flexibility or rigidity, to meet the unique requirements of different pipeline systems.
3. Metal Components (e.g., Stainless Steel, Aluminum Alloys):
Metal components, such as stainless steel or aluminum alloys, are often integrated into modern mechanical pipe plugs for added strength and longevity.
● These materials provide exceptional resistance to corrosion, abrasion, and mechanical wear, ensuring prolonged service life in demanding conditions.
● By incorporating metal components, mechanical pipe plugs can withstand higher pressures and temperatures while maintaining tight seals and preventing leaks.
Case Studies: Real-world Applications of Mechanical Pipe Plugs
1. Oil and Gas Industry
Challenges: The oil and gas industry faced a corroded section in their pipeline, necessitating repairs. Traditional methods would lead to extensive excavation and downtime, disrupting operations and incurring significant costs.
Solution: Mechanical pipe plugs were deployed to isolate the damaged section without shutting down the entire pipeline. This allowed for targeted repairs to be conducted efficiently, minimizing downtime and operational disruptions.
2. Municipal Water Supply Sector
Challenges: A water treatment plant encountered a sudden leak in one of its main distribution lines, posing a risk to public health and safety.
Solution: Mechanical pipe plugs were deployed to temporarily seal the leak, allowing for emergency repairs without interrupting water service to the community.
3. Construction Industry
Challenges: During the installation of a new sewage system, existing sewer lines needed to be temporarily sealed to prevent contamination.
Solution: Mechanical pipe plugs effectively block off the affected sections, allowing construction work to proceed safely and efficiently while maintaining compliance with environmental regulations.
4. Chemical Processing Industry
Challenges: A chemical processing plant faced the need to isolate sections of pipelines for maintenance without disrupting ongoing operations.
Solution: Mechanical pipe plugs provided a quick and efficient solution to temporarily seal off the pipelines, allowing for targeted maintenance activities to be carried out without interrupting production.
Key Features Of Mechanical Pipe Plug
For any pipeline maintenance, Petersen Products' mechanical pipe plugs stand out for their exceptional quality and performance.
Key features that make these types of pipe plugs a preferred choice:
1. Pressure Resistance:
● This products are engineered to withstand high pressures, making them suitable for a wide range of applications.
● These plugs are designed to maintain a tight seal even under extreme pressure conditions, ensuring reliable performance in demanding environments.
2. Easy Installation:
● Designed with user convenience in mind, these plugs can be quickly and easily installed without the need for specialized tools or equipment.
● The simple installation process minimizes downtime and ensures efficient maintenance operations.
3. Adaptability:
● Whether it's for temporary isolation, pressure testing, or emergency repairs, these are large-diameter mechanical pipe plugs that can accommodate a wide range of applications.
● Their versatility allows operators to address different maintenance challenges effectively, enhancing overall efficiency and flexibility.
4. Durability:
● Built to last, these high-pressure pipe plugs are constructed from high-quality materials that withstand the rigors of pipeline maintenance.
● These plugs are resistant to corrosion, abrasion, and wear, ensuring long-term durability and reliability in harsh operating conditions.
Best Practices for Installing and Using Mechanical Pipe Plugs
For optimal performance and longevity of mechanical pipe plugs, follow these best practices:
1. Ensure the pipe and plug surfaces are clean and free of debris.
2. Lubricate the plug and pipe surfaces to facilitate smooth installation.
3. Gradually insert the plug into the pipe, avoiding abrupt movements.
4. Use a mallet or hammer to gently tap the plug into place until a secure seal is achieved.
5. Avoid over-tightening the plug to prevent damage to the pipe or plug.
6. Regularly inspect plugs for signs of wear or damage and replace them as needed.
7. Store plugs in a cool, dry place away from direct sunlight to prevent degradation of materials.
Common Challenges and Solutions
Mechanical pipe plugs are invaluable assets in pipeline maintenance, but they can encounter common challenges. By addressing these challenges with proactive solutions, operators can maximize the effectiveness and reliability of mechanical pipe plugs in pipeline maintenance operations-
1. Improper Fitment:
● Issue: Inaccurate sizing or irregular pipe shapes may lead to improper fitment of the plug.
● Solution: Use sizing charts or measurement tools to select the correct plug size. Consider using expandable plugs for irregular pipe shapes.
2. Leakage:
● Issue: Despite installation, leaks may occur due to insufficient sealing or pipe damage.
● Solution: Ensure proper lubrication and installation techniques. Inspect the pipe for damage before installation. Consider using higher-pressure plugs for improved sealing.
3. Plug Dislodgement:
● Issue: Plugs may become dislodged during operation, especially in high-pressure environments.
● Solution: Use retention devices or mechanical locks to secure the plug in place. Monitor pressure levels regularly to detect potential dislodgement early.
4. Material Degradation:
● Issue: Exposure to harsh chemicals or environmental conditions may degrade plug materials over time.
● Solution: Select plugs made from durable materials resistant to corrosion and wear. Implement regular inspections and maintenance to identify signs of degradation and replace plugs as needed.
5. Temperature Extremes:
● Issue: Extreme temperatures can affect plug performance, leading to expansion, contraction, or material fatigue.
● Solution: Choose plugs rated for the anticipated temperature range. Consider using heat-resistant materials for high-temperature applications. Monitor temperature fluctuations and adjust plug selection accordingly.
Industry Compliance and Standards
Ensuring industry compliance and adhering to strict standards is crucial when buying mechanical pipe plugs. The certified and quality products ensure the safety and reliability of pipeline systems.
Petersen Products is the best platform where you can get certified products. We offer the best plugs and other Plumbing and Industrial Pipeline Products that meet industry regulations and standards to prevent leaks, failures, and other operational risks.
Adherence to Industry Standards
Petersen Products upholds stringent industry standards to guarantee the quality and performance of our mechanical pipe plugs. We proudly hold certifications such as ISO 9001:2015, demonstrating our commitment to excellence in manufacturing.
Additionally, our custom manufacturing capabilities allow for tailoring pipe plugs to specific project requirements, ensuring precise fit and optimal functionality. The unwavering dedication to quality is reflected in the comprehensive quality statement offered by us. We guide every aspect of the production process by following the industry regulations and standards.
Pipe Specifications for Reference
While Petersen Products specializes in mechanical pipe plugs and does not sell pipes, we offer guidance on selecting the best pipes based on plugging needs. Our website offers various pipe specifications, including pipe threading standards, nominal pipe sizes, copper tubing sizes, SDR pipe references, and more.
In selecting pipe plugs, customers can reference pipe specifications available under the Pipe Specifications for Reference section. These specifications provide valuable guidance in choosing the right plug size, material, and configuration for their specific pipeline needs. Aligning with industry standards and utilizing accurate pipe specifications, customers can make informed decisions to ensure the proper functioning and integrity of their pipeline systems.
The Future of Mechanical Pipe Plugs: Emerging Trends and Technologies
As technology continues to advance, the world of mechanical pipe plugs is poised for exciting innovations and advancements.
Some key trends and technologies include:
1. IoT Integration: Smart plugs equipped with sensors and connectivity capabilities can provide real-time data on pipeline conditions, allowing for proactive maintenance and predictive analytics. These smart plugs can detect leaks, monitor pressure levels, and even self-adjust to optimize sealing performance, reducing the need for manual intervention and minimizing downtime.
2. Advanced Materials: Advancements in material science are also driving innovation in mechanical pipe plug design. The development of novel materials with enhanced durability, chemical resistance, and temperature tolerance will result in plugs that can withstand even harsher operating conditions.
3. Advanced Manufacturing: Advancements in manufacturing techniques, such as 3D printing, may enable the production of custom-designed plugs with intricate geometries and optimized performance characteristics.
Conclusion
One of three things occurs when you use a pipe plug:
(1) closing off a pipeline or opening's flow;
(2) avoiding the pipeline's current flow, or
(3) checking for leaks in an existing pipeline or conducting a low-pressure air test on a new pipeline before putting it into service.
Mechanical pipe plugs play a crucial role in pipeline maintenance, offering reliability, versatility, and efficiency.
Are you looking for different types of pipe plugs? Well, Petersen Products is the right place for you!
Petersen Products stands out as a reliable source, adhering to stringent industry standards like ISO 9001:2015 and offering custom manufacturing capabilities to meet specific project needs. Noticing the emerging trends, readers must leverage this knowledge for effective pipeline maintenance, ensuring the integrity and functionality of their systems for years to come.
Some Key Takeaways:
1. Ensure safety and reliability with certified and compliant mechanical pipe plugs.
2. Petersen Products adheres to stringent industry standards like ISO 9001:2015.
3. Utilize provided pipe specifications for selecting optimal pipes.
4. Stay updated on emerging trends like IoT integration for enhanced pipeline maintenance.