Why Regular Gas Line Pressure Testing is Essential for Safety

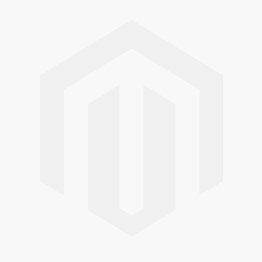
Gas line safety is crucial in industrial settings to ensure facilities operate safely and efficiently. Industrial gas lines, which are used in various industries such as manufacturing, energy, and utilities, must be examined and maintained on a regular basis to avoid costly and harmful leaks or system failures. The gas line pressure test is an important part of this safety routine because it detects leaks or structural problems before they become a challenge.
A pressure test of a gas line involves applying a set amount of pressure to the gas lines and looking for any drops that could signal a leak. This testing not only improves worker safety but also guarantees compliance to demanding industry rules, thereby preserving assets, staff, and production deadlines. Regular gas line pressure testing allows businesses to achieve safer, more reliable gas line performance while avoiding costly downtime and regulatory penalties.
What is a Gas Line Pressure Test?
A gas line pressure test is a process for determining the safety and strength of a gas line system. This test involves using controlled pressure to the gas line and monitoring it to see if there are any pressure drops. If the pressure drops, it can indicate there is a leak or a weak spot in the line. Pressure testing detects leaks, confirms line strength, and ensures system integrity, keeping the gas line safe and reliable.
Importance of Regular Gas Line Pressure Testing
Regular pressure testing a gas line is essential for maintaining the safety of gas lines in residential, commercial, and industrial environments. These tests prevent hazardous leaks, protecting people and the environment from harmful gas exposure.
Regular testing also ensures that gas line systems meet with regulatory and safety standards, which are required by many companies and municipal regulations. Pressure testing not only increases safety, but it also helps property owners and businesses comply with essential standards.
How to Pressure Test a Gas Line?
A gas line pressure test is required to detect leaks and maintain the safety of gas systems. Here is a step-by-step instruction for performing a pressure test safely.
Tools & Equipment Required:
- Pressure gauge
- Wrenches and Pipe Fittings
- Soap solution for leak detection
- Low Pressure Gas Plugs
- Pressure testing pump
Step by Step Gas Line Pressure Test Process:
- Turn Off the Gas Supply - Turn off the gas supply entirely to ensure safety throughout the test. This prevents unintended gas flow.
- Purge the Gas Line - Before starting the test, use a Low-Pressure Gas Plug to safely remove any remaining gas. Petersen's 113 Series plugs are suitable for this, with a high-quality Ballistic Nylon outer ply that resists hydrocarbons and a flexible design that can secure even out-of-round pipelines.
- Set Up the Test Equipment - Connect the pressure gauge and any other required fittings to the gas line. Ensure that all connections are secure and leak-free.
- Pressurize the Line - To pressurize the gas line, use a testing pump or a regulated pressure source. Recommended pressure levels vary so always follow the standard guidelines by manufacturer.
- Monitor Pressure Levels - Allow the pressure to stabilize and monitor the gauge for any drops. A pressure drop usually indicates a leak in the line.
- Inspect for Leaks - If there is a pressure drop, apply a soap solution to joints and fittings to find the source of the leak. Bubbles will reveal the source of the leak.
By following these steps and using reliable equipment, you can safely and successfully pressure test a gas line, resulting in a leak-free, secure system.
Common Issues Identified During Gas Line Pressure Testing
Gas line pressure testing is useful at detecting a variety of problems that, if left untreated, could result in system failures, potential risks, or expensive repairs. Common issues detected during a pressure test include:
- Minor Leaks: Even minor leaks can pose serious issues over time, potentially resulting in dangerous gas buildup.
- Corrosion: Rust and corrosion damage pipes, increasing the risk of leaks and pressure loss.
- Weak or Damaged Sections: Areas of the pipe that have weakened due to age, wear, or damage can become incapable to withstand regular operating conditions.
By identifying and addressing these concerns early on, property owners and managers can avoid costly repairs, system breakdowns, and preserve residents' health and safety.
Frequency of Gas Line Pressure Testing: When Should It Be Done?
The frequency with which a gas line pressure test should be performed depends on the setting and system being used.
- Residential - Residential gas lines should be inspected on an annual or biannual basis to ensure their safety.
- Commercial/Industrial - Commercial/industrial environments often require more regular testing due to industry standards and the amount of gas used. Monthly or quarterly inspections are frequently recommended for such facilities.
Signs that immediate testing is needed
Regardless of regular schedules, the following signs may indicate the need for rapid gas line pressure testing:
- Unusual gas smells or the smell of rotten eggs
- Visible corrosion or damaged pipe sections
- Unexplained pressure drops or fluctuations in gas line performance
Regular testing is critical for maintaining the safety and functionality of gas systems in any setting, ensuring compliance and providing peace of mind for both owners and occupants.
Conclusion
Regular gas line pressure testing is important for maintaining safety, complying to compliance regulations, and preventing costly repairs. By monitoring gas lines on a regular basis, property owners can find leaks early, avoid potential hazards, and extend the life of their systems. Prioritizing gas line maintenance protects not just residents, but also assets.
Disclaimer: The information may be used but with no warranty or liability. This information is believed to be correct but should always be double checked with alternative sources. Strictly adhere to and follow all applicable national and local regulations and practices.
Regardless of these comments, it is always necessary to read and understand manufactures instructions and local regulations prior to using any item.