24" Sewer Main Repair with Nitrogen Filled Inflatable Line Stop

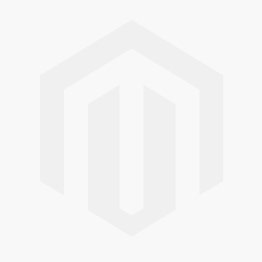
Failing sanitary sewer lines can often be repaired with conventional methods—especially in residential areas there are usually plenty of options for isolation and rerouting. But it was a different scenario in a recent failure near Chicago; a cracked 24-inch steel pipe sewer main was close to a lift station in a congested, very active industrial area. The main served a large steel mill and a chemical plant that couldn’t afford downtime. So the cracked and failing pipe had to be repaired quickly in a way that kept the plants running. Isolating the pipe called for a large inflatable plug that could be inserted through a relatively small hot tap. “The size of main was one of the things that made this tricky,” says Ryan Stacey, owner of RJ Stacey Ltd. “The main was at 35 psi operating pressure, but it was 24 inches, which meant 1,000s of pounds of force. Ideally, we needed a very sophisticated, high-capacity plug that could hold in a smooth pipe, through a hole of no more than 12 inches—that’s a pretty tall order.”
But Stacey has quite a bit of experience when it comes to plugging lines; “We’re specialists,” he explains. “We’re one of the few companies nationwide that specialize in line stopping and isolation, and we’ve been doing it for fifteen years.” Inflatable line plugs are an unusual order for most contractors, but Stacey has used them in dozens of different situations. In this case, his first choice for supplier was Wisconsin-based Petersen Products. “I know (President) Phil Lundman quite well by now,” he says. “And he has an unusual ability to work from my description of the situation and sketches, and create just what is needed without detailed plans. Plus, they deliver quickly, which was important for this project.”
When working out an isolation plan, Stacey has to keep the subject system’s design specifications in mind, and the operating parameters. “For permanent fixtures, like flanges and other installations, of course we need to work up to design specs. But for a temporary installation like this plug, it’s better to work within expected operating parameters.”
In this case, Petersen Products was able to craft an inflatable plug of ethylene propylene diene monomer (EDPM—a type of synthetic rubber), reinforced with ballistic nylon, and since Stacey had an 11.5-inch shell cutter on hand, the plug was made to slip through a hole this size. “I’m really glad they could make this plug fit through a relatively small hole,” says Stacey. “If we’d had to tap, say, an 18-inch hole, this job would have been much more expensive because it would have required a split T tapping saddle, and maybe not doable due to space.” All this custom work was done at record speed, and the plug was drop shipped and on the job site just eight days after the order was placed—and this included a 24-hour test, with the plug inflated to 1.5 times design psi at the factory, to guarantee it was shipped in perfect order. “I was impressed,” Stacey says. “And it worked even better than I anticipated—basically, it was perfect.”
Better Than Perfect?
After hot tapping, the plug was inserted and inflated with nitrogen tanks brought to the site. “We always use nitrogen when we’re isolating gas lines,” Stacey explains. “It’s convenient, and it’s an inert gas, so there’s no possibility that it will create an explosive mixture. Of course this wasn’t a gas line, but nitrogen was a good choice because of the possible presence of sewer gases.”
RJ Stacey crews used nitrogen to inflate the plug to 52 psi, enough in theory to hold the plug in place and allow downstream work. A ‘bottle watch’ man was stationed on site to monitor the plug’s pressure and refill from it from tanks as needed. But in practice, no refilling was needed. The Petersen plug stayed in place for five days, and never needed to be repressurized. Essentially, it held perfectly—this perfect plug allowed repairs to take place inside the lift station serving the mill and chemical plant. One big concern was keeping nasty solid matter from interfering with work. “Before our plug went in, trash pumps—large-capacity pumps that grind up solid matter—had been running continually for days, due to the leaks,” Stacey says. “But with the plug in place that stopped immediately.” Also, as repair work was done, Stacey installed several 8-inch pipes that were hot tapped into the 24-inch line upstream of the plug, to reroute waste.
There was even an ironic side effect of the plug holding perfectly, without refilling. “We installed the plug in the morning, when it was cool," Stacey says. “And with that done, pressure in the nitrogen tank was at 1,900 psi. Later in the day, as the sun hit the tank and heated it, pressure actually increased from 1,900 psi to about 2,100 psi—we joked that we might come out ahead on nitrogen on this project!”
Reusable
After use, Stacey was able to withdraw the plug; “There were no complications on withdrawal, it came out easily, considering the small hole size,” he says. “Of course, we’re not so worried about it on the way out, since the project is done, but we do like to keep them on hand for reuse if possible.”
Once withdrawn, Stacey sends used plugs back to Petersen for inspection, pressure testing (as described above), and rebundling. He estimates he has a dozen different inflatable bags in storage, ready for reuse. Of course, they’re sized and designed for particular situations, but those configurations do repeat on occasion, and Stacey has reused bags and he says they hold up well. “My guess is that, with refurbishing between jobs, they can be used indefinitely.”
Typically, inflatable plugs are used in small diameter, high pressure pipes, as found in industrial plants and refineries. But they’ve also proven to be very useful in large diameter sewers, water lines, and other situations usually associated with municipalities. In this case, an inflatable plug satisfied a particular need very efficiently, and two plants employing thousands of people were able to operate continually over five days, without service interruption, while complex lift station repairs were carried out successfully.
# # #
Angus W. Stocking, L.S. is a licensed land surveyor who has been writing about infrastructure since 2002.