An Inflatable Plug Works Better Than Bypassing Pumping When Closing Off A 60-Inch Penstock

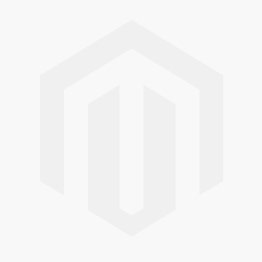
When Brian Simon, a project manager at Grace-Titan DVBE (based in Redding, California) first looked at the Potter Valley Bypass job it looked difficult, but straightforward. Grace-Titan was being asked to remove a section of the penstock that supplies Pacific Gas & Electric's (PGE) Potter Valley hydroelectric plant and install a Y-branch. But that meant that the five-foot diameter penstock had to be shut down temporarily... and that's where things got complicated. The penstock and the gate valve that's supposed to close it down when needed, are both more than a hundred years old. Because of the age and condition of the gate valve, Grace-Titan was told to expect flow leakage as high as 1,200 gpm and to account for this preparation and design.
"The operators did a fantastic job when closing the gate valve," says Brian Simon, the Grace-Titan project manager in charge of the Potter Valley Bypass, "in fact, as it turned out, flow rates topped out at about 400 gpm."
So Simon had to find a way to plug the penstock downstream of the valve and keep pressures relatively low. The water could have been diverted with pumps, but there were serious downsides to that approach. "If we'd used pumps, there would always have been the possibility that they'd fail," he explains. And that would have exposed downstream workers, who would be welding inside the penstock, to unacceptable safety risks. It would also affect power plant operations, so pumps would have to monitored 24 hours a day, seven days a week by two men-a Grace-Titan employee and a PG&E representative. The cost would be enormous and wouldn't completely eliminate the safety risks.
Instead, a physical block was needed and an existing 18-inch manway presented the best opportunity. "We hadn't done anything like this before, so we did some research," says Simon, "and it seemed like an inflatable plug was the way to go." Simon selected Petersen Products Company (based in Fredonia, Wisconsin), an American firm that has been making specialty pipe supplies since 1916. Petersen fabricated a plug that could be folded for insertion through the manway, then inflated with low-pressure pumped water to fill and block the penstock.
"We opened up the manway and inserted the plug-it took three of us to control it as we lowered it in," says Simon. Once in place, the plug was tethered with dual aircraft cables and inflated with a diaphragm pump and controller purchased from Petersen. "It didn't actually seal well the first time we inflated it," says Simon, "probably because of oversized rivets in the old pipe. So we hauled it back out, repositioned it, and pumped it up again." This time, the plug sealed well and held for the entire seven weeks of the project.
With the plug in place, the flow backed up to the manway and through a fitting made by Andre Revel, a Grace-Titan consultant for the leak control procedure. This fitting diverted the water to the tailrace in a controlled manner. The Grace-Titan crew was able to work safely, without having to rely on a powered system with moving parts.
To monitor water levels at the manway, Simon installed a sight glass connected to a dip tube. The water levels in the penstock were calibrated to the sight glass, providing a way to quickly check levels and thus pressure buildup.
Simon says the plug definitely saved money and was probably instrumental in getting the job in the first place. "I would say that proposing the plug helped us get the job, because PG&E liked our plan. And it saved a lot of money, for us and the plant, because we saved the labor of having two people on the site continually, for seven weeks-that could have been over a $100,000 just in labor. Plus, of course, the plug was safer because we didn't have to worry about pumps failing. It also eased environmental concerns regarding pump or generator refueling."
Because this was a first project with new technology, Petersen worked with Grace-Titan on the design and deployment of the plug. Design calculations from Grace-Titan were checked by Petersen's engineers and a Petersen representative was on site for the deployment. They were a great resource on this first project." He says that Grace-Titan is definitely looking for more inflatable plug applications and hopes to put their new expertise to work soon.
After seven weeks, the plug was drained by the diaphragm pump and removed with the help of a forklift. It had held without failure, and Simon says it looked good; "It's in excellent shape, no damage at all," he says, "we could reuse it."
Safer and easier are great qualities in a new technology, especially when that solution is less expensive as well. By being open to new ideas and doing a little research, Grace-Titan has developed useful new capabilities that they'll put to work on future projects.
Angus W. Stocking, L.S.