An Inflatable Tunnel Grout Seal Stops Flooding of the World’s Largest Undeveloped Uranium Mine

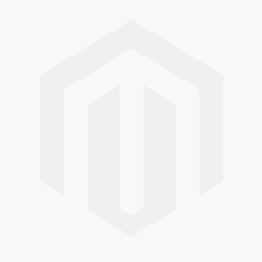
Cameco Cigar Lake Uranium Mine
The Cigar Lake Mine, located in the Athabasca Basin of Northern Saskatchewan, Canada, is sitting on the world's largest undeveloped high-grade uranium deposit in the world. Operated and majority-owned by Cameco Corporation, Cigar Lake is expected to eventually provide more than 10% of the world's mined uranium.
But to extract the uranium ore, Cameco has to overcome significant technical challenges. For one thing, the main orebody is 430 to 480 meters (1,410 to 1,575 feet) beneath the surface. And, above the orebody, a soft, highly permeable clay zone, and lots of groundwater, complicate all ordinary mine procedures. Operators are also dealing with the 'typical' problems of uranium mining, such as handling and storing ore and limiting radiation exposure. To overcome these difficult conditions, Cameco will be using a jet boring mining method involving artificial freezing to stabilize ground layers, subsurface use of tunnel boring machines, and installation of multiple cased pilot holes. When everything is in place, a rotating high-pressure jet will be used to dislodge ore and pull it up the pilot holes.
Overcoming Flooding With an Inflatable Seal
Mine development has been plagued by flooding, and an inflow via fissure in August 2008 flooded the 420- meter level (420L) and completely stopped work. To stop the flooding, Cameco had to create a barrier in that level that would completely seal off the area of inflow. "In 2007," says Cameco Project Engineer Brian Dixon, "we developed a method of creating underground barriers from the surface by pouring cementitious material through drilled holes. Unfortunately, that method wouldn't work here because the material would have spilled into the adjacent mine shaft, preventing accumulation of material and successful formation of a barrier." Instead, Cameco employed a more complex, but ultimately successful, method that relied on a custom-made, inflatable tunnel seal (ITS) from Petersen Products Company, customized remotely operated vehicles (ROV), and extensive underwater debris removal.
Work began by clearing out debris and also by removing mechanical infrastructure, such as piping and ventilation ducting. "Everything needed to be removed prior to the inflation of the seal," explains Dixon, "to ensure that water did not have a way to pass between the infrastructure and the seal, once it was inflated." With debris removed, two tricky problems remained. The ITS, which is a cylindrical plug designed to expand to approximately seven meters when inflated, had to be positioned and oriented precisely by an ROV, and then filled from the surface not once, but twice: once with water to check position, and then with a custom formulated grout to form a permanent seal. To complicate matters, construction-class ROVs couldn't be used because Cigar Lake's shaft diameter is too small to allow entry; instead, smaller inspectionclass ROVs had to be adapted for the work. To position the ITS, and for other work, new holes were drilled from the surface to a tunnel in the flooded 420L. A wireline truck then lowered a cable down one of the new holes to the 420L, where it was captured by the ROV. The cable was then pulled to a point where it could surface in the shaft, where the Petersen ITS was attached. A shaft winch and the ROV, guided by the ROV's visual system and a sonar system developed by Cameco, were then used to pull the ITS back into the shaft and maneuver it into the correct location.
With the ITS in place, the next step was to inflate it with water to check positioning and sealing. A coil tubing unit, outfitted with a special mating receptacle, was lowered down an adjacent new drill hole. The ROV made the connection, the bag's packaging system was released and water was pumped in. When the ITS was fully inflated, the sonar system and the ROV's cameras were used to check fit and placement. "If the bag hadn't been correctly placed, there were positioning straps and a deflation system available," explains Dixon, "So we could have corrected its position if required." But in the event, the ITS filled and sealed the shaft perfectly. So, using the same tubing unit, the ITS was then filled with a specially formulated grout, which displaced the water in the bag through a relief port system. Grout was pumped in until it was observed flowing out the top of the bag, then the grout was allowed to setup, effectively plugging the shaft. To further seal off all inflow, more grout was pumped into a series of drilled holes east of the bag. Eventually, the fissure that allowed inflow was fractured with perforating guns and pressure grouted to insure against any further flooding. In October 2009, after all grout was set, Cameco reported that the water inflow had "been remediated", and in February 2010, after dewatering, crews reentered the working level of the mine, 480 meters (1,575 feet) beneath the surface and 60 meters (197 feet) below the previously flooded 420L level. Since then, the main shaft has been refurbished and Cameco has announced that underground development should be completed by October, 2010.
"Uranium is an important resource that will help meet the world's energy needs," said Petersen Products Company CEO Phil Lundman, "and we are very proud that our products are helping to develop the world's richest remaining source of this vital product. Our inflatable plugs and bags have 'filled a need' in extreme situations all over the world, but this very deep, technically challenging installation is a milestone. Congratulations to Cameco for accomplishing such an amazing infrastructure project, and getting the Cigar Lake Mine back on track!"
# # #
Angus W. Stocking, L.S. is a licensed land surveyor now writing full time about infrastructure topics.