Plugging a 60" Sewer with Inflatable Plug for 5 Months

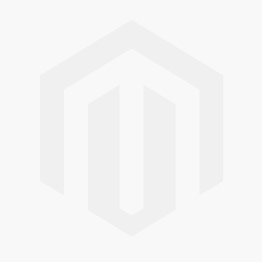
With a population of about 140,000, Hollywood is Florida’s twelfth largest city. Most of its growth took place in the 1950s and 1960s and so, like many cities, Hollywood is now coping with a legacy of aging, and in some cases, crumbling infrastructure. A good example is the city’s gravity-fed main sewer transmission line, 6,000 feet of 60-inch diameter lined concrete. “Mostly there was a lot of failure and erosion at the bottom, plus failing joints and infiltration around manholes,” says Underground Utility Manager Ron Bolton. “And much of the line runs directly under main city streets.”
To address the failing line and to cope with continuing expansion, Hollywood built another 66-inch main line, parallel to the first. But the original line couldn’t simply be abandoned; its capacity is still very much needed. So Hollywood needed a way to dewater and repair the old concrete pipe, while a new fiberglass lining was installed. Most of the flow could be diverted into the new parallel line, but that still left a lot of water. “We estimate that infiltration alone was letting in a few hundred thousand gallons daily,” Bolton explains.
Hollywood needed a way to eliminate infiltration flows during the sewer rehabilitation project without tearing up city streets. They turned to a solution from Petersen Products, specialists in inflatable plugs. “We’ve used inflatable plugs on several occasions, and they’ve always worked well for us,” Bolton says. Still, an inflatable bag sized to plug a 60-inch concrete line would have to be quite effective to hold back hundreds of thousands of gallons daily. The utilities department placed the order and hoped for the best.
The Plug That Held Back a Flood
Petersen has been making inflatable plugs for a variety of purposes for decades—their plugs and specialized tapping solutions have been used in high pressure gas lines, large tunnels, mine dewatering operations, and in more exotic scenarios. The company works with client specifications to design plugs that will work, and in this case they produced a plug made of ballistic nylon reinforced with an external layer of polyurethane, customized with dual inflation/deflation ports that could accommodate inflation with water or grout or, if higher pressures were needed, with air. Deflated, the plug is just 17 inches in diameter, allowing insertion through a manhole. All the pumps, valves, regulators, and monitors needed to inflate and deflate the plug safely and effectively were custom matched to the plug and provided by Petersen.
Inflated, the bag is more than twelve feet long, and about eight feet of that was in direct contact with the pipe, providing the seal. “Even deflated, it’s a big, bulky plug,” says Operations Manager William Feliciano. “We moved it into place with a crane, and, at the end of the project, we pulled it out with a backhoe.
In some cases, plugs are test inflated outside of pipes to check dimensions at under 10% of rated pressure. But here, “We were concerned that a bag this size, without the constraints of the pipe, would distort or stretch,” Bolton says.
After some dewatering by pumping, the plug was inserted 1,000 feet above the treatment plant, and was left in place for five months. Initial inflation was with water. “You have to fill with water first to make shape and get a good seal, and to make sure the plug holds where you want it to be,” Feliciano explains. But, “Water is heavy though, and can stretch out the plug if it’s in place for a long time.”
In this case, the plug was to be in place for five months. So, after inflation with water, conversion attachments were placed at the dual ports, and air was used to displace the water. Air pressure was raised to 12 psi and monitored continually.
So how well did the plug work? “It stood up to a few pounds of head pressure for five months, and held very tight,” Bolton says. “We found that we had to add a little air every few weeks, which isn’t difficult, and had no failures of any kind.” At time of removal, the plug was holding back enough water to fill the pipe about halfway, going back more than 5,000 feet.
The plug installation permitted relining work in relatively dry conditions and kept infiltration out of the treatment plant for that entire time. That last bit is important; “We saved more than the cost of the plug just in treatment costs,” Bolton says.
Both lines are now in service and infiltration has been minimized. “We were getting close to our treatable permitted limit,” Bolton says.“So having the opportunity to reduce inflow and infiltration is very helpful. And having both lines in place has been great.”
So sometimes, a plugged sewer line is just what’s needed.
# # #
Angus W. Stocking, L.S. is a licensed land surveyor who has been writing about infrastructure since 2002.