What is Hot Tapping?

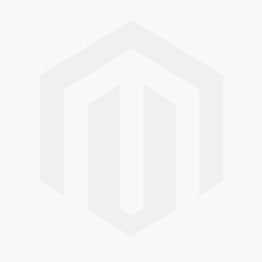
Hot tapping is a process used to attach a branch connection to a pipeline without needing to depressurize or disrupt normal operations. The technique is also used to isolate sections of pipe for maintenance by plugging or stopping the line. Hot tapping is also referred to as line tapping, pressure tapping, pressure cutting, and side cutting.
Whether conducting maintenance or adding a new section of pipeline, the benefit of hot tapping lies in that it allows pipeline owners and operators to isolate and bypass sections of pipeline without shutting down their entire system and halting production, resulting in costly downtime.When to use a hot tap
Hot tapping is a serious operation that can be dangerous if not done correctly. For that reason, we recommend only using a hot tap when it is impractical to take the entire system out of service or there is no other option for completing repairs or adding a new pipeline branch. Once all other options have been evaluated and ruled out, you can turn to hot tapping.
For example, when it comes to natural gas transmission and distribution systems, it is often necessary to relocate or expand existing pipelines, repair existing valves, and install new valves. In the past it has been common to shut down a portion of the system, vent the gas within the isolated segment, and purge the pipeline with inert gas to ensure a safe connection.
This process creates both economic and environmental problems. By venting the gas, you lose product and release harmful methane emissions, and by shutting down a portion of the system, you may cause interruptions in gas service to customers. Because of these issues, hot tapping is a practical and cost effective alternative. It allows you to perform the pipeline maintenance or expansion without venting the gas or cutting off service to customers.
How hot tapping works
The hot tapping process involves attaching branch connections and cutting holes into the operating pipeline without interruption of gas flow, and with no release or loss of product. Hot taps permit new additions to existing systems, the insertion of devices into the flow stream, permanent or temporary bypasses, and is the preparatory stage for line plugging with inflatable, temporary balloon plugs.
There are hot tapping systems available for most pipeline sizes, material, and pressure ratings. The typical components of a hot tap machine include a drill, the fitting, and a valve. The drill cuts a hole in the pipeline wall and the fitting wraps around the entire pipe and forms a sealed connection between the hot tap machine and the hole in the pipeline wall. The valve can be either a block valve or control valve for the new connection and allows the section of the pipeline wall that was cut out by the drilling machine to be removed after the cutting operation.
Hot tap systems can be vertical or horizontal and can be used at any angle around the pipe that allows enough room to install the valve, fitting, and tapping machine. Depending on the size of your pipe, there are even lightweight hot tapping machines that can be installed and operated by a single person.
Benefits of hot tapping
As we already mentioned, there are several economic and environmental benefits to using a hot tap instead of a system shut down. Hot tapping avoids releasing harmful gases into the atmosphere, doesn’t waste gas, and doesn’t interrupt service to customers. Additionally, you can avoid time consuming cutting, realignment, and rewelding of pipeline sections and reduce your costs associated with planning and coordinating a complete system or section shut down.
Want to know if using a hot tap is the best choice for your pipeline project? Contact the Petersen team for more guidance and information.